No internet connection.
All search filters on the page have been cleared., your search has been saved..
- Sign in to my profile My Profile

Toward the Deming Prize: The Case of Tata Steel (A)
- By: Arnab Laha & Gouttam Doutta
- Publisher: Indian Institute of Management, Ahmedabad
- Publication year: 2014
- Online pub date: January 04, 2017
- Discipline: Quality Management , Creativity & Innovation in Business
- DOI: https:// doi. org/10.4135/9781473994188
- Keywords: control chart , customer relationship management , quality improvement , staff , statistical control , top management , total quality management Show all Show less
- Contains: Content Partners | Teaching Notes Length: 5,802 words Region: Southern Asia Country: India Industry: Manufacture of basic metals Originally Published In: Laha , A. & Doutta , G. ( 2014 ). Toward the Deming Prize: The Case of Tata Steel (A). PROD0297. Ahmedabad : Indian Institute of Management, Ahmedabad . Organization: Tata Group Type: Direct case info Organization Size: Large info Online ISBN: 9781473994188 Copyright: Certain material used with permission of Indian Institute of Management, Ahmedabad. © 2014. All rights reserved. More information Less information
Teaching Notes
Supplementary resources.
The case series deals with the successful initiation of Tata Steel in various fields. This resulted in Tata Steel becoming lowest cost steel producer in the world. The case series documents the various initiations.
The website had been checked several times earlier, almost hourly, for the last couple of days in anticipation of the good news. Gupta was on an official tour and had been anxiously waiting for the good news. For the last few years, he had put in an enormous amount of work preparing Tata Steel for this prestigious award. He was feeling extremely nervous. What if Tata Steel failed to make the cut? But as the phone rang and he saw his deputy’s telephone number, his heart leapt up – maybe it was good news at last. And there it was – the most coveted Deming Application Prize ( Exhibit 1 ) for 2008 had been awarded to Tata Steel. The taxing days of preparation had now got the ending they deserved. It was a defining moment in the 100-year old history of Tata Steel. Gupta could anticipate the celebrations that would happen in the days to come.
Sen, Gupta’s senior, had made preparations much in advance to communicate this achievement to the employees and the public as soon as possible. Within a few hours of the announcement, most employees and the public of the small steel town of Jamshedpur knew of Tata Steel’s achievement in the field of quality. At the headquarters, the jubilant Managing Director, Muthuraman, raised a toast in honor of all the employees who had made this achievement possible (refer to the MD’s Deming Prize acceptance speech – Exhibit 2 ). He also lauded the tremendous team work and dedication of all his colleagues. Muthuraman personally wrote letters to thank the consultants who had guided Tata Steel. He also wrote to Tata Steel’s customers informing them about their winning the award and thanking them for their support to Tata Steel. The Deming Application Prize triumph marked the beginning of a new era at Tata Steel.
Four years down the line, Bhadhuri, the chief manager for TQM activities, was getting ready to face another prestigious award examination – the Deming Grand Prize previously known as the Japan Quality medal. This examination was supposed to be even more rigorous than the earlier Deming Application Prize. He could feel the building up of the same energy and excitement throughout the plant as that seen before the Deming Application Prize examination. He wanted to see this excitement grow. In the intervening four years since the Deming Application Prize, he had sometimes felt the enthusiasm towards TQM slackening a bit. But this examination had put the zest back at the same level as it had been four years ago. Sen, the Vice President responsible for TQM and Bhadhuri’s senior, knew that it would happen this way as Tata Steel was a “Do” company. The employees were extremely task oriented and would put in whatever it took and more, to achieve a milestone. However, he realized that it could also be a hindrance to sustain the enthusiasm for quality. How many more prestigious awards similar to the Deming Grand Prize were there to win? How would the company sustain its enthusiasm for quality once the Deming Grand Prize was won? Bhadhuri knew that the initial quality improvements were significant and kept the employees enthused, but as time progressed, the quality improvements were not that large and it was quite natural for the employees to lose some of their enthusiasm. He felt the real challenge would be to keep the employees focused on quality even after the Deming Grand Prize examination was over. Bhadhuri was worried that once significant quality improvements had been made, it might be quite difficult to sustain the employees’ enthusiasm to improve quality further and thus may lead to an erosion of the TQM culture. The real challenge, he realized, would arise a few years into the future. For now the Deming Grand Prize examination had helped.
The TATA Group Background
The TATA group today is an example of the industrial development of India from the end of the nineteenth century. It was Jamsetji Tata’s vision to make India a developed nation. Today, the group is a conglomeration of 98 different businesses spread over one hundred countries with an annual revenue of $ 67.4 billion and employing 390,000 employees. The Indian Hotels Company Limited (popularly known as The Taj Group of Hotels) started in 1902, the steel business in Jamshedpur started in 1907 (now known as Tata Steel), the power business in 1912 (now known as TATA Power), the airline business in 1932 (now known as Air India), higher education (now known as Indian Institute of Science, Bangalore), and automobiles in 1945 (now known as TATA Motors) are examples of how the vision of Jamsetji Tata changed the industrial scenario in India even before Independence. It is the largest employer in India in the private sector and continues to lead with the same commitment towards social and community responsibilities and is known for its strong values and ethics.
The business and operations of the TATA group are spread over 114 companies and subsidiaries and they specialize in seven core sectors: Materials, Engineering, Information Technology and Communications, Energy, Services, Consumer Products, and Chemicals. For further information, please visit www.tata.com
Started in 1907, Tata Steel today is one of the largest steel makers in the world. The Tata Steel group had an annual turnover of USD 22.8 billion in the financial year 2011, with over 80,000 thousand employees across five continents. ( Exhibit 3 shows the recent financial statistics of Tata Steel.) It is now one of the world’s most geographically dispersed steel producers. It has operations in all five continents, in 26 countries, and a commercial presence in over 50 different countries across the globe. It produces annual crude steel of 28 million tons per annum. The major production facilities of the company are located in India, the UK, the Netherlands, Thailand, Singapore, China, and Australia.
Tata Steel’s vision is to be the steel industry benchmark in the world through its commitment to excellence, innovative approach, ethical values, social responsibility, continuous improvement, openness, and transparency. In the early 80s, the company’s operation was primarily focused only in India; it was the pre-liberalized Indian economy. However, after liberalization, the company realized that in order to compete in the global market, it needed to improve the quality of its product.
Towards TQM (1991–2011)
“Values stronger than Steel” – a tagline adopted by Tata Steel in recent times – represented its aspiration to be a company driven by values in all its endeavors. Trust and values form a very important foundation for any organization aspiring to become a global leader in quality. Dr. W. Edwards Deming, the American statistician who is largely credited for the dramatic quality improvements of Japanese products in the 1950s and in whose honor the prestigious awards for quality given by the Union of Japanese Scientists and Engineers (JUSE) are named, had repeatedly stressed the importance of trust and shared values in building an organization capable of delivering high quality products consistently over the long term. The inculcation of the shared values across the company was an important step towards the goal of being a quality leader in steel manufacturing.
The journey of Tata Steel towards becoming an organization which was focused on quality was not quick. The company undertook a gradual but rigorous process of change with the goal of making quality a central part of all its decision making processes. In a competitive global business scenario where quality was the sole determinant of business success, Tata Steel embraced Total Quality Management wholeheartedly. Throughout this transformation process, the company undertook a series of initiatives that helped create a strong belief in TQM among its stakeholders. A large employee base of nearly 40,000 differently skilled employees ranging from Ph.D.s in Metallurgy to non-matriculate workers spread all across the country were engaged through training which helped them understand what TQM was and how they would benefit by adopting TQM in their activities. The TQM vehicles (Policy Management, Daily Management, Quality Assurance, and Employee Involvement) and TQM methodologies along with internal review mechanisms and robust TQM Training and Development programs created a foundation for Total Quality Management at Tata Steel. According to several senior officials at Tata Steel, practicing TQM over the years had led to significant improvements in several areas like product quality, skilled labor, and well informed consumers, regulated distribution network etc. and also had a significant impact on the bottom-line.
In the year 1991, India embarked upon economic reforms and the liberalization of its economy. These steps by the Indian government opened the largely protected Indian business organizations to the strong winds of global competition. In the period prior to the economic liberalization, steel was a scarce commodity and demand for steel far exceeded its supply. But, with economic liberalization, customers had the choice of importing steel without depending on domestic producers. Thus domestic steel manufacturers now had serious competition and they needed to improve productivity and cut product cost to make it competitive with the global manufacturers, to remain in business. With supply now exceeding demand, quality became the main determinant of business success. It was therefore quite natural that the management at Tata Steel decided to embrace TQM as a tool for business success. The “ Chalta Hai ” (loosely translated means ‘It’s ok’) approach then prevalent in the company was costly, as it induced many failures and discouraged assimilation of learning from these failures, which could be used to prevent future failures. With TQM came a focus on processes which helped in the eradication of the “ Chalta Hai ” attitude over a period of time.
In 1995, the Tata group created the JRD QV award named after its late chairman JRD Tata for creating awareness about the importance of quality and to achieve and sustain excellence and leadership in the marketplace. Soon thereafter, the TATA Business Excellence Model (TBEM) was created along the lines of the Malcolm Baldrige National Quality Award of the United States of America (USA), for all the businesses run by the TATA group ( Exhibit 4 ). The Malcolm Baldrige National Quality Award was set up by the government of the USA through its enactment of the Malcolm Baldrige National Quality Improvement Act of 1987. The award aimed to stimulate American companies to improve quality and productivity by recognizing those companies which are able to achieve substantial improvements on these aspects. The other objective of establishing this award was to provide guidelines and criteria for quality improvement that could be used by organizations for evaluating their own quality improvement efforts. The TBEM therefore served the purpose of helping the Tata Group companies improve their quality and productivity. With an aim of achieving business goals and enhancing quality, Tata Quality Management Services (TQMS) was formed to provide a helping hand to the Tata companies in key areas like innovation, corporate governance and ethics, safety, training and assessment, and educational excellence.
During the l990’s, Tata Steel faced considerable challenges in project management which could be partially attributed to the prevalent “ Chalta Hai ” attitude. Around the year 1997, the company created a vision of making a world-class cold-rolling mill complex (CRM) at the lowest project cost within a fixed implementation time. With thorough planning, and building a team which exhibited exceptional team spirit, dedication and bonding, they implemented the CRM project in a world record time of 26 months. In 2000, Tata Steel won the JRD QV award. World Steel Dynamics (WSD), a renowned industry analyst firm in the US, declared Tata Steel to be the world’s lowest cost producer of steel in the following year. An innovative culture that encouraged learning was the next goal. This was accomplished by engaging the employees through training, seminars, implementation of suggestion and feedback schemes for the employees, including employees as important participants in discussions, and making sure that the company’s vision became the common vision for every individual employee.
The next few years were extremely important for Tata Steel. During this period, the company adopted quality improvement approaches consistent with their vision to become a global quality leader. The Plan-Do-Check-Adjust (PDCA) cycle was adopted as the main vehicle for problem solving and quality improvement, along with other tools. Improvement teams were set up across the organization for improving quality on a continuous basis. Philosophies like the Theory of Constraints (TOC) were adopted and extensive efforts were made to train the employees of the company regarding TOC and TQM. Policy Management (Hoshin Kanri) and Daily Management helped the company to move in the desired direction. The then MD, Muthuraman commented later: “2000 to 2005 were years of intense strategic thinking about the company’s future, formulating and initiating plans for the company’s organic growth in Jamshedpur and initiation of green-field projects in India.”
Exhibit 4 represents the growth process of TQM at Tata Steel. It can be divided into three distinct parts: Introduction, Establishing TQM for business, and Embedding TQM in the DNA. The first part was building awareness with several tools like Value Engineering, Quality Circles, and Total Preventive Maintenance. In the second part of the TQM Journey (2000-2004), TQM became the core competency for overall competitiveness. During this time Tata Steel stood first among all Tata companies in the Tata Business Excellence Model (explained in Exhibit 5 ). In the third part after the Deming Prize (2008 till today), the company started to make TQM a part of the minutest cell of the organization, somewhat like the DNA of the human body. The company could sense the changing business need and it also decided to respond appropriately in each step (see Exhibit 6 ).
However, it is interesting to know the story of the application process of TQM. In the mid-2000s when the initial inspection for the company’s readiness to apply for the Deming Application Prize was conducted by the Japanese consultants, they determined that the company had not understood the essence of TQM. They suggested that the company should not apply for the prize immediately but instead focus on ingraining quality in all their activities. In the subsequent diagnosis, the trial run of the schedule-B examination for the prize, which included on-site investigations and Q & A with the senior management, did not go well. No Q-C story was presented and it failed to convince the consultants’ team again. On being asked how long would it take for the company to be ready for prize, one of the members of this team answered – “By 200x?”
Finally in 2008, the consultants’ team gave Tata Steel the green signal for applying for the prize. The Deming Application Prize examination was extremely rigorous. It involved 26 examiners and took over one and a half months. Since Tata Steel was fully ready for the examination, it could satisfy the examiners team on all its queries. Muthuraman commented to his colleagues after the completion of the examination that “it was like facing the matriculation examination again.” All the documents used for the examination were archived for future use which proved to be very useful for the Deming Grand Prize application process.
On 6 October 2008, Tata Steel was declared to be the sole winner of the Deming Application Prize for the year 2008. It was the most coveted endorsement for the continuous quality and performance improvement that Tata Steel had demonstrated in recent years.
TQM – In Pursuit of Excellence
The transformation at Tata Steel and their adoption of TQM was achieved in stages. Over a cup of coffee, Mishra, a senior executive in the TQM department, recalled that the first thing the top management did was to address the attitude of the people and bring about a positive change in it. They also simultaneously attempted to change the mindset of the management so that a positive culture was created, which could support the harmonious working of teams. By the end of the 1990’s, the cost-oriented management system was gradually superseded by a flexible, customer friendly approach. The concept of internal customer got strongly rooted in the company. By offering its customers quality services and helping them achieve their business objectives, Tata Steel soon became a much sought after ‘supplier of choice’ for leading companies in diverse market sectors. It may be noted that one of the important points emphasized by Deming was that ‘improving Quality automatically results in improving productivity’.
The company strove hard to provide more value to its customers. One example of this was the help provided by Tata Steel’s application support engineers for solving complex problems of the consumers. This led to the creation of deep bonds with its customers and Tata Steel became the ‘company of choice’ for many of its customers. Its engineers also started helping individual house builders in the efficient sourcing of the products they needed. The uniform pricing of Tata Steel products at all the outlets across the country was appreciated greatly by the customers and it allowed them to plan effectively for their projects. Tata Steel, which was now capable of producing ultra-high quality steel, also helped its customers with their import substitution strategy. All these actions helped establish a strong brand for Tata Steel products.
Mishra noted that absence of fear, working with zest, a pioneering spirit, and delivering the best has always been part of the work culture at Tata Steel. He felt that the adoption of TQM led to the optimization of the company’s performance and overall employee development. He enthusiastically pointed out how he had adopted the “Daily Management” practiced at Tata Steel in his personal life. He had two young children at home with whom he needed to spend some quality time. For this purpose, he created a chart where he put a Red or a Green dot every day. The Green dot signified that he had given quality time to his children on a particular day whereas the Red dot indicated he hadn’t done so. This helped him give quality time to his children at home on a daily basis. Another example he gave was the discipline he had imbibed to prevent his mailbox size from exceeding the given limit. He now archives or deletes some mails on a daily basis according to their level of importance. This has eliminated the “mail box overflow” problem for him.
Over the past 100 years, Tata Steel has always prided itself as one of the most ethical organizations in the country. This has played an important part in its becoming the company it is today. Honesty, integrity, and respect for rules were considered as the core values of every employee and all individuals associated with Tata Steel. We caught a glimpse of it inside the Tata Steel plant. The hurly-burly of the chaotic traffic outside its plant gates vanished immediately on entering the gates. The traffic flowed very smoothly, strictly following the rules laid down. Even the contract vehicle drivers asked their passengers to put on the seat belts on entering the plant. Everyone took special care not to violate the speed limits and parked their cars in the right slots. As we mentioned our experience to Chakraborty, a senior executive, his face beamed with joy and he commented, “Every time I enter the gates of Tata Steel, I feel it is a different world.”
TQM in Manufacturing
Tata Steel has focused on making its entire steel-making process eco-friendly and economical, using world-class technology. The focus on employee safety has been a cornerstone of management action in recent years. Even visitors are given a detailed briefing about the safety procedures before entering the facility. We were provided with protective gear, and detailed instructions (including demonstrations using video recordings) were given to us on how to use them. In our interaction with Mishra – who heads the LD-2 steel making division and is himself a Six Sigma Black Belt – we got to know that with the introduction of TQM, an efficient workflow with well controlled parameters has been made a norm throughout the plant. The organization has become much more aligned towards achieving its stated objectives that has brought in continuity. The company has also been successful in automating some of the processes helping it to produce very high quality of steel.
Generally, steel making processes are dusty and environmentally unfavorable, but to our surprise, we found the plant, including the Blast Furnace area, to be quite clean. (Refer to Exhibit 7 for the complete steel making process.) Quite clearly, the employees have imbibed a culture of cleanliness and safety. We came across Kaizen boards at different work areas on which various quality and safety improvement efforts were documented and shared with fellow employees. This has helped to preserve knowledge.
The Control Chart is a simple statistical process control tool based on Shewhart’s “Theory of Variation” that helps operators and process supervisors determine whether the process is in statistical control or not. Shewhart said that variation can be decomposed into two types – one due to “chance” or random causes and the other due to “assignable” causes. A “chance” cause of variation is very difficult to reduce while an “assignable” cause of variation can be quickly eliminated from the process, if detected. A process that operates with “chance” causes only is said to be “in statistical control” or “in-control” while one that operates with “assignable” causes of variation present is said to be “not in statistical control” or simply, “out-of-control”. A control chart helps in detecting the presence of “assignable” causes of variation quickly. Each critical parameter of the process is monitored using a control chart. If any critical parameter value shifts substantially from its desired value then the corresponding control chart shows an out-of-control condition. The operators and process supervisors can then find out what caused this condition and bring the process back in-control by eliminating the problem cause. At various places in the steel manufacturing process we found control charts being used effectively by the process operators and supervisors. “Decision Trees” are drawn for many known assignable causes which make detection of assignable causes an easier task. Decision Tree ( Exhibit 8 ) is a formal management technique which guides a decision maker in uncertain situations. It provides alternatives and compares different situations and different alternatives.
Mishra remarked that “Quality is our prime driver for sustenance” and mentioned that “all scorecards we use are linked with Quality parameters”. As an example, he said that more than 30 per cent reduction had happened in downgrading off-heats. This could be attributed to increased quality awareness amongst the workers at Tata Steel and the training received by them. This resulted in uniformity of information among all levels of management. He also said that a lot of weight is given to safety and accident free operations. This helps in creating a healthy environment. As we waited in the room to meet Sen, we could hear the daily “dispatcher briefing” going on. The “dispatcher briefing” happens every morning with the senior management at Tata Steel attending. The importance given to safety can be gauged from the fact that the first item on the agenda was a briefing by a plant in-charge on a small accident that resulted in a hand injury to an employee. In fact, the Japanese consultants working with Tata Steel for preparation towards the Deming Prize placed tremendous importance on safety. Accidents caused by unsafe procedures could cause not only severe monetary loss but could also demoralize and instill fear in the minds of the employees which could lead to poor quality of products. The consultants advised the top management to take ownership of any accident in the company – small or big. This helped a lot in creating a safe working environment for all its employees.
Gupta recalled his discussion with the eminent quality thinker Dr. Noriaki Kano who said that there are two types of companies in the world – A-type and J-type. A-type organizations are driven by inorganic growth through mergers and acquisitions and innovation, which requires huge investments. In contrast, the J-type companies are propelled by engagement with employees and continuous improvement and need far lesser investments. J-type companies succeed not by doing any extraordinary things, but by doing simple things extraordinarily.
Engaged Employees
Quality is ALL about people. It is the engaged well trained workforce that helps organizations achieve high quality performance. Tata Steel was no exception. The management at Tata Steel engaged the workforce with a lot of support and motivation along with appropriate training to help them achieve the quality goals. They were involved in serious discussions and decision making about their production processes. Suggestion schemes and small group activities (SGA) helped production workers to try out their own ideas in improving their own processes. Through the adoption of Kaizen, the company was moving towards a culture of free flow of knowledge within the organization. This was in sharp contrast to the knowledge-retention culture that was largely present in the company in earlier times. Earlier, knowledge was treated as private information to be handed down from the “godfather” to his favourite protégé. This impeded quick dissemination of any information related to improvement in quality along with other undesirable cultural fallouts. Employee satisfaction was measured periodically through ESAT surveys done by an independent agency which was taken seriously by management for further action. The findings of the last survey indicated that the employees were enthused and that there was now more role clarity.
“Tata Steel has a robust talent pipeline,” stated Sen. He said that there was a talent review system within the company which understood the individual’s potential and also tried to measure their delivery against their promised goals. The management looked for relative performances and the rewards were given in monetary form. The incentive and reward structure was supported and communicated by the top management. An implicit categorization of employees at the officer level existed, and their career advancement was totally based on their capabilities.
For any enterprise, there is a great deal of problem solving that is needed in its day-to-day functioning. The “Problem Solving and Task Achieving” (PSTA) team formed an important part of Quality Assurance at Tata Steel. It helped in resolving intricate problems and also helped manage the knowledge that was generated. Continuous personnel development and enhancement of problem solving capabilities were the two major activities of PSTA. “Problem solving experts aren’t full time employees but they take this as additional work along with their routine job,” stated Srivastava, who led the PSTA team. The problem solving experts enjoyed doing this activity and some were very proficient. “Roughly 50% of the experts have done two or more projects,” added Srivastava.
The PSTA team, supported by an efficient IT system, helped in the sharing of information among the process-heads. This helped them to quickly identify experts for a particular problem and to get them involved in problem solving. A big repository of different projects done by “Green Belts” and “Black Belts” has been built for quick reference which can be easily accessed by the employees. We saw some excellent project reports using Design of Experiments (DoE) and Response Surface Methodology (RSM) done earlier for solving quality problems and for improving the quality of some products.
“Kar Vijay Har Shikhar” (KVHS) was an initiative which was focused at EBITDA improvements through operational improvement and integration of all quality improvement initiatives. The strategy for “prioritizing projects” under KVHS was to arrange them on the basis of 3-I: Impact, Investment, and Implementation Time. Projects with high impact, low investment, and low implementation time were the best for KVHS initiatives. Lochan – chief of the KVHS initiative, described a couple of cases of ‘quick wins’. Recently, the KVHS team was assigned the responsibility of helping to improve the productivity of a process. Through empirical research, the KVHS team found that each time-off taken by operators for a toilet break was of about 15 minutes duration. On digging deeper they found that the reason for this was that the toilet was located far away from the place of work. A ‘quick win’ was achieved by providing a cycle to the workers which could be used for going to the toilet. This reduced the duration of time-off significantly and productivity increased considerably. In another project it was found that crane operators took frequent breaks during their job causing delay and loss of productive time. On looking for the cause, it was found that the cabins were extremely hot and uncomfortable causing the crane operators to step down whenever there was no work. The KVHS team found a ‘quick win’ for this problem. They recommended that the crane operators’ cabins be air-conditioned which led to dramatic reduction in the delay and an increase in productivity.
Impact on Supply Chain
Tata Steel has been successfully backing its brands with strong quality. The monthly corporate quality report was followed by the MD with interest. Chakraborty said that there was a time when the objective was just to ‘produce more’ irrespective of demand while now the production was done only when an order was placed. He said that the quality initiatives had benefited the customers through consistency in product performance and timely delivery. Another benefit has been that the working capital requirement of Tata Steel has been reduced significantly. It was now possible to deliver in small lots and the stock keeping units (SKUs) had been reduced to reduce complexities.
Sen thought that there was a need for more work to be done in the B-2-B (Business-to-Business) space in order to create a win-win relationship with the customers. Some companies had started working together with Tata Steel recently as they understood the benefits and realized that “They have invested in us.” Through supplier value management programs, the company aimed at building enduring relationships with its suppliers also.
TQM Journey – Next Steps
The long term vision of Tata Steel was to be the ‘best in quality and service’ said Chakraborty. His group has been working towards the extension of the TBEM by incorporating community services like local education, water and sanitation, agriculture, etc. He viewed the winning of the Deming Application Prize as an important milestone. Also, the improvement activities being undertaken for the Deming Grand Prize examination would help the company to reach higher levels of efficiency. However he felt that the passion for excellence at Tata Steel was not award-driven. He did not agree with the suggestion that India is a “low-quality country” and said that it was an incorrect perception. He gave the example of the Taj Mahal which is one of the most architecturally beautiful monuments in the world, made completely in India and that too many centuries ago, when engineering was not as advanced as it is today. He argued that the fervor for excellence is inherent in the Indian psyche. Tata Steel as a company had the vision of being able to provide world-class quality to international customers in India in the near future.
Sen said that the journey towards excellence has seen an increased quality awareness, expertise, and deeper understanding of systems and processes. He said that his team is working on the “Tata Steel Way” which would be a codification of the best practices developed at Tata Steel. The “Tata Steel Way” would aim at making Tata Steel a knowledge-based organization which strives incessantly towards building customer value with the spirit of continuous improvement and synergy to achieve their goals. Discussing the importance of the Tata Steel way, Bhadhuri, who has been with the company since the 1980’s recalled that a senior colleague of his used to say that all knowledge about the process was in his ‘Red diary’.
“Tata Steel is an excellent place to work and a great learning experience to cherish,” said Gupta. Comparing his experience at Tata Steel India and Tata Steel Europe he said that organizations need to stabilize and mature before being able to fully adopt TQM. The adoption of TQM at Tata Steel India has been facilitated by a mature workforce and stabilized operations. “The challenge in the journey ahead will be to change from being an enthusiasm-driven to a commitment-driven company,” said Chakraborty. One of the major points of focus is to come closer to the end customers and understand their requirements better. He said that there has been a sea change in the top management approach to quality. In the past, the top management was not involved in quality matters at all. Today, the Managing Director of the company heads a Quality-board which reviews quality management practices every two months. The importance of embedding TQM in all operations of the company cannot be overstated. There have been many new entrants in the Tata Steel family post the winning of the Deming Application Prize. They need to imbibe the culture at Tata Steel and the TQM journey cannot go to the next level without getting their ‘buy-ins’. “The Deming Grand Prize examination has greatly helped in this regard,” said Bhaduri. The ‘Tata Steel Way’ would be of great help in this respect as it would quickly educate new entrants into the culture and work processes at the company. In the times to come, the company will endeavor to make the whole company a team by ensuring that employees from all levels feel comfortable to work with another employee from any other level at Tata Steel.
Bhadhuri was sitting in his office and preparing for a meeting with Sen on what challenges Tata Steel would face in keeping itself quality focused and striving for quality-led business excellence in the next ten years. While the quality paradigm had successfully spread all across the organization, he would like these practices to be ingrained in the DNA of the company. How would this be achieved? Would the company be able to further enhance the quality improvement efforts easily without the motivation to achieve a prestigious award like the Deming Grand Prize? The company employed unskilled workmen in its mines and collieries who may not have even high school education leave alone doctorates in Metallurgical engineering for its research and development centers. How would the newcomers in the organization ranging from unskilled workmen to specialized professionals be developed continuously for achieving quality in all their endeavors?
Bhaduri was also thinking about how the experience of Tata Steel India’s quality journey could be replicated in Tata Steel Europe and Tata Steel Thailand? Would cultural factors play a role in this?
This case was prepared for inclusion in Sage Business Cases primarily as a basis for classroom discussion or self-study, and is not meant to illustrate either effective or ineffective management styles. Nothing herein shall be deemed to be an endorsement of any kind. This case is for scholarly, educational, or personal use only within your university, and cannot be forwarded outside the university or used for other commercial purposes.
2024 Sage Publications, Inc. All Rights Reserved
The case studies on Sage Business Cases are designed and optimized for online learning. Please refer to the online version of this case to fully experience any video, data embeds, spreadsheets, slides, or other resources that may be included.
Exhibit 1: The Deming Application Prize
In 1950, the Union of Japanese Scientists and Engineers (JUSE) invited Dr. W. Edwards Deming, (an American consultant, also a well-known “Quality Guru”) to Japan to conduct a series of lectures and seminars on “The Basic Principles of Statistical Quality Control” for the Japanese industries. The Japanese were extremely overwhelmed by his teachings. Subsequently, to honor Dr. Deming’s contribution, JUSE formed a prize called The Deming Prize.
The Deming Application Prize (DAP) is an award presented yearly to a company that has made distinguishing improvements as a result of applying TQM. Notwithstanding the type, size or origins, any company in the world can apply for the Prize. Only those companies, who efficiently develop and deploy TQM methods in all aspects to fulfill their objectives, are eligible for the DAP. The applicant companies go through a chain of examinations carried out by the DAP Subcommittee. The Deming Prize Committee then selects those companies, who score the passing points or more in the examination and awards them the prize. As a matter of fact, the number of likely recipients of the prize, in a year, can be unlimited. In recent years, many Indian Companies like TVS Motor Co., Mahindra & Mahindra, Tata Steel, etc. have won the Deming Application Prize.
Source: www.deming.org (Retrieved on December 19, 2012)
Exhibit 2: Acceptance speech by MD of Tata Steel at Tokyo on receiving the Deming Award:
“Konbanwa, Mina–sama. ( Good Evening everyone. )
On October 6, 2008 when I got the news that Tata Steel has been nominated to receive the Deming Application Prize, my first reaction was one of great joy. I was completely overwhelmed and overjoyed; so were my colleagues; so were all the employees of Tata Steel.
We knew that we are the only steel company, outside of Japan, to win the Deming Application Prize, so far. We also knew that we are the only steel company in the world, with operations spanning from raw materials to finished products to ever win this Prize. It was worthy of rejoice and pride.
After the initial feeling of great happiness sank in, some questions began to appear in my mind. Did we really deserve this Award? Was the question paper too simple? Were the examiners too lenient? Or was it, by chance, that the questions that were asked of us were the only questions that we had fully prepared answers for. After all, we have all been students, we have all been through examinations and we know that such things can happen!
Slowly, I began to realize that it is not because we are perfect that we are getting the Deming Prize. It is because we have taken the first steps, first firm and sure steps towards quality movement and because a large number of people in the entire organization are involved in that movement that we are being given this prestigious award.
Our efforts to challenge the Deming Prize and the questions the Deming Examiners asked us made us humble and made us realize that we now have a tool and a system with which we can improve everything we do on a continuous and predictable basis, that our results would be based on our efforts and that we would be able to overcome any obstacles put on us by the external environment.
I believe that this Prize is coming to us at the right time with financial and economic crisis all around the world. We believe that our work and our efforts to get this Prize and the work and efforts that we will do to justify our winning this Prize will make us succeed even in the midst of this crisis and make us a better organization than what we are today.
I would like to sincerely thank the Deming Examiners for giving us this Award. I would also like to thank our consultants, headed by Dr. Noriaki Kano for teaching us and guiding us in our work and in our efforts.
Arigato – Gozaimashita. ( Thank you very much. )”
Source: Tata Steel
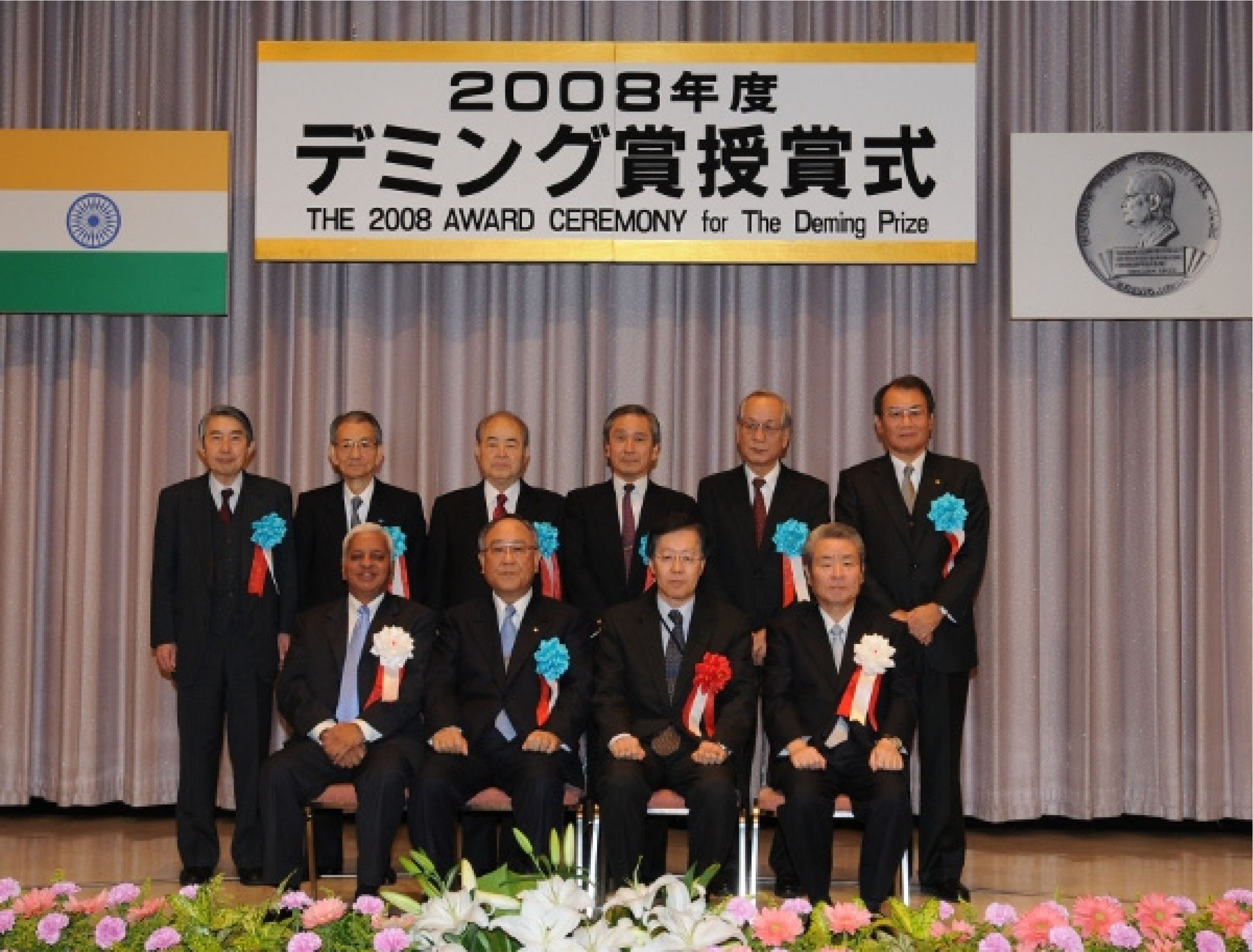
Source: Photo Ref: http://www.juse.or.jp/e/deming/53/ (Retrieved on December 19, 2012)
Exhibit 3: TATA Steel’s Recent Financial Statistics
(Figures in Rs. Millions)
Source: Tata Steel Annual Reports (FY-07 to FY-11)

Exhibit 4: TQM journey
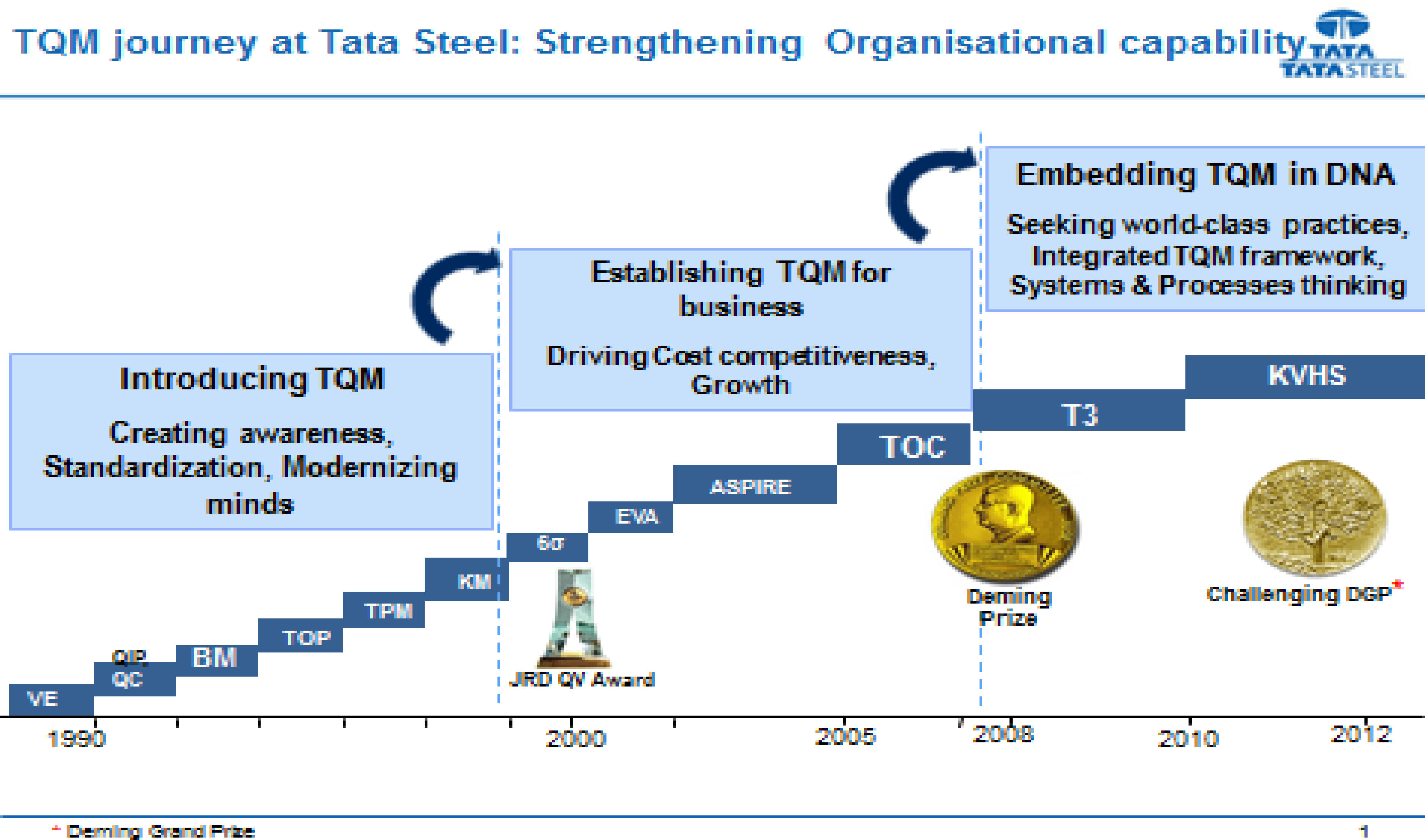
Exhibit 5: Tata Business Excellence Model
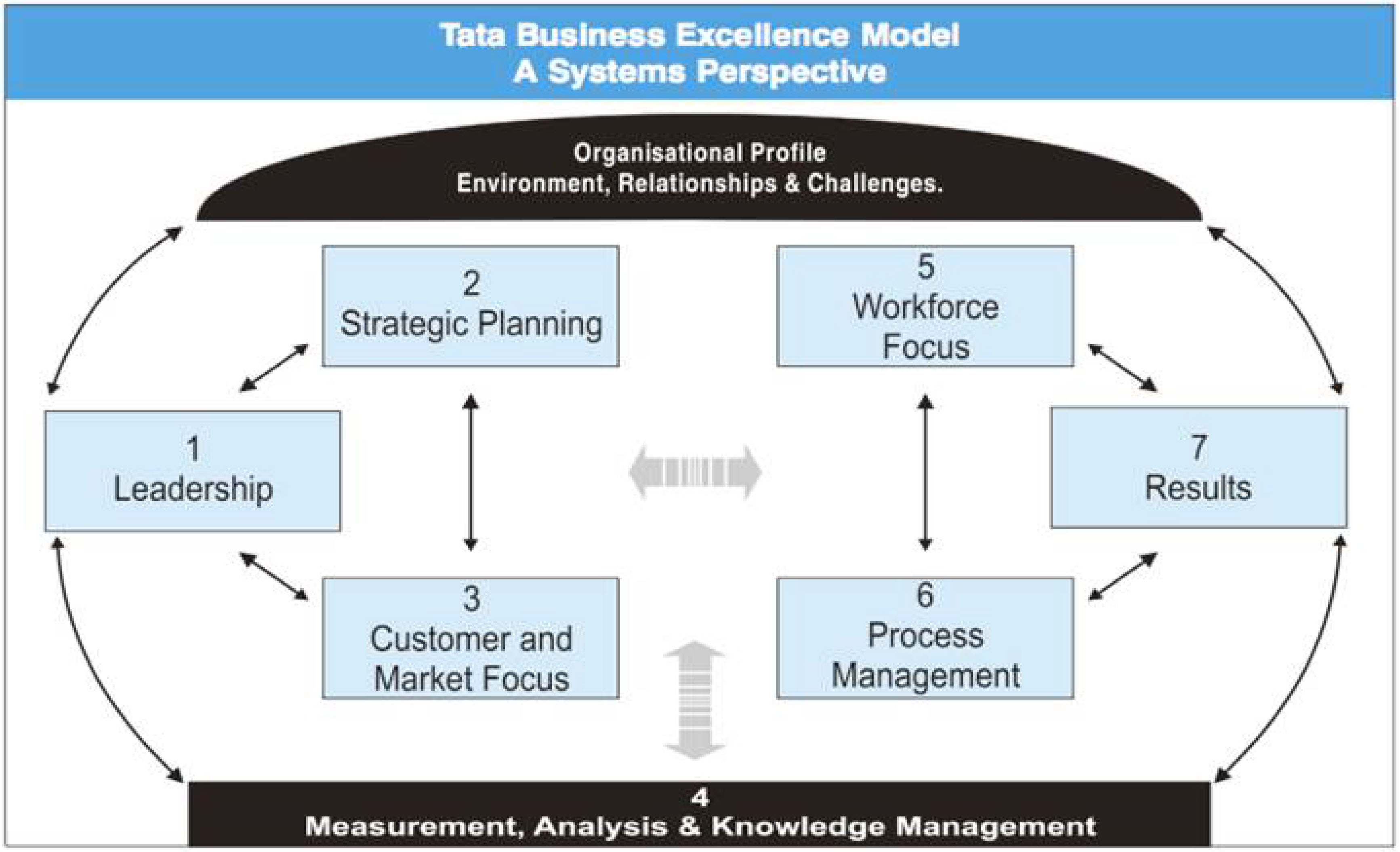
Source: http://tqmswebsite.tataquality.com (Retrieved on December 19, 2012)
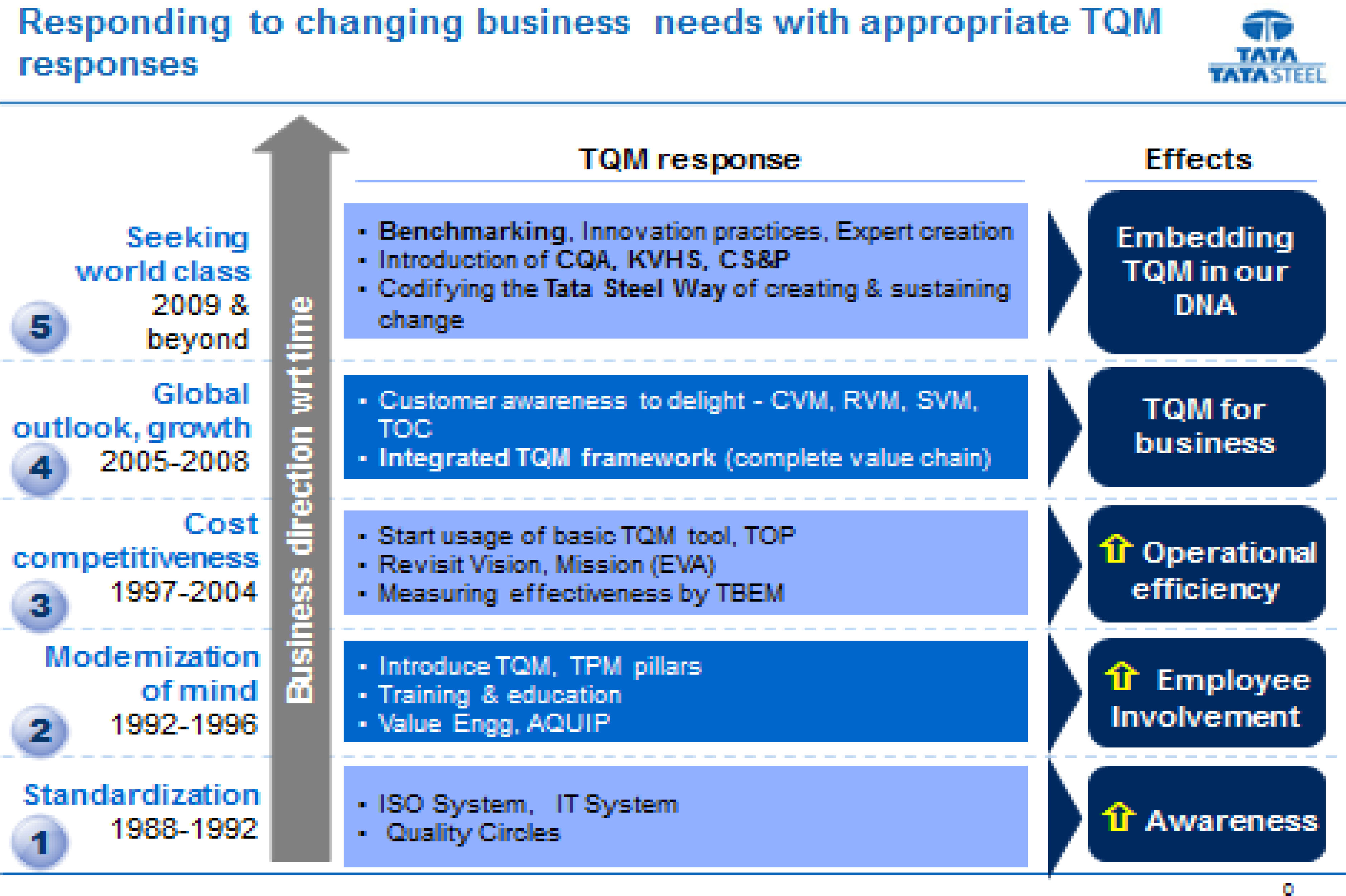
Source: Tata Steel Internal documents
Exhibit 7: Process of Steel Manufacturing
Steel manufacturing is a multi-step process. There is a lot of technology and expertise behind it. The following gives an overview of the different stages involved in the production of steel.
Iron Making
Iron ore is the raw ingredient needed to initiate the process, which has to be blended with fluxes (Metallurgical Agents) consisting of Dolomite, Dunnite and Limestone. In coke ovens, Coal is processed into Coke to make it impurity-free. The Stamp Charging Technology enables the use of lower quality of coal to form high quality coke with significantly improved strength.
Since the iron ore fines are not suitable for direct use in the Blast Furnace, they are “sintered”. Sintering is a process where the mixture of the well proportioned iron ore particles, the fluxes, and coke breeze is heated under protective conditions to produce a semi molten mass in order to increase the strength. On solidification, the sinter thus formed is cooled, stored and then sent to the blast furnace.
Blast Furnace
The Blast Furnace is a huge reactor used for the production of liquid iron called Hot Metal. Iron oxide, present in the iron, is reduced by Coke and Carbon Monoxide (CO) that are charged inside the furnace.
Coke is used to get high temperatures needed to facilitate the reduction process. On combustion it generates Carbon Monoxide, which acts as the reducing agent and converts iron oxide into molten iron. Fluxes are used to make low melting slag (residue resulting from smelting). After draining the impure slag, the molten hot metal is tapped from the furnace at approximately 1500 ºC and then purified into Steel in the LD-Converters.
Steel Making
Steel making is the process of selective oxidation of impurities of hot metal in the Steel Melting Shops namely LD-1 and LD-2 Steelmaking shops.
The hot metal produced in the blast furnace is carbon saturated iron with Silicon, Sulphur, Phosphorus and Manganese components. In the LD-Converters, there is a pear-shaped furnace where the hot metal is refined by removing the impurities and is stored for some time. An 8-10 meter long, water-cooled lance is lowered which blows a high pressure stream of oxygen that separates the impurities. The heat produced due to the chemical reaction is sufficient to raise the temperature of hot metal to a molten steel temperature of approximately 1600 ºC.
Continuous Casting
The next phase is the highly energy and cost-efficient Continuous Casting method which involves converting molten steel into semi finished products, namely, billets or slabs. In the continuous casting process, tundish, mold and cooling sprays are arranged in such a way that hot liquid steel is poured from the tundish and the coagulated product is removed continuously. The billets, having an approximate 5’’x5’’or 7’’x7’’ dimension, are processed into long products such as wire rods, forging quality bars, etc. while the slabs with a width of around 150-250 mm are processed into various types of flat products such as sheets and plates to cater to sectors such as automobiles, railways, construction and others.
Hot Strip Mill (HSM)
A Hot Strip Mill produces a strip with reduced thickness by rolling the slabs formed in the continuous casting process. In the HSM, the slabs are heated at a very high temperature (above 1000 ºC) and are then fed to a roughing mill and rolled out to make them thinner. They are then coiled and uncoiled and elongated before being driven to the finishing mill. After being cooled by a Spray Cooling System, the thin strip is recoiled and readied for dispatch.
Cold Rolling Mill (CRM)
The coils from the HSM are fed into the CRM. Here, they are reduced more in thickness and given characteristics according to customer requirements. Steel is cleaned and made more malleable or ductile through pickling (removing impurities) and annealing (a metallurgic process that changes the properties of material). In the Skin Pass mill, the coils are further tempered to improve the surface finish. To remove corrosion, the strips are dipped in a bath of molten zinc in order to give it a uniform protective lining through the continuous hot dip galvanizing process. Through the rolling lines, the strips undergo edge trimming and are then sent for inspection to control the product quality.
Source: Tata Iron and Steel Co. Ltd – Steel Making Process- http://tatasteelindia.com/products-and-processes/processes/steel-making-process.asp http://steel.nic.in/glossary.htm
(Retrieved on December 19, 2012)
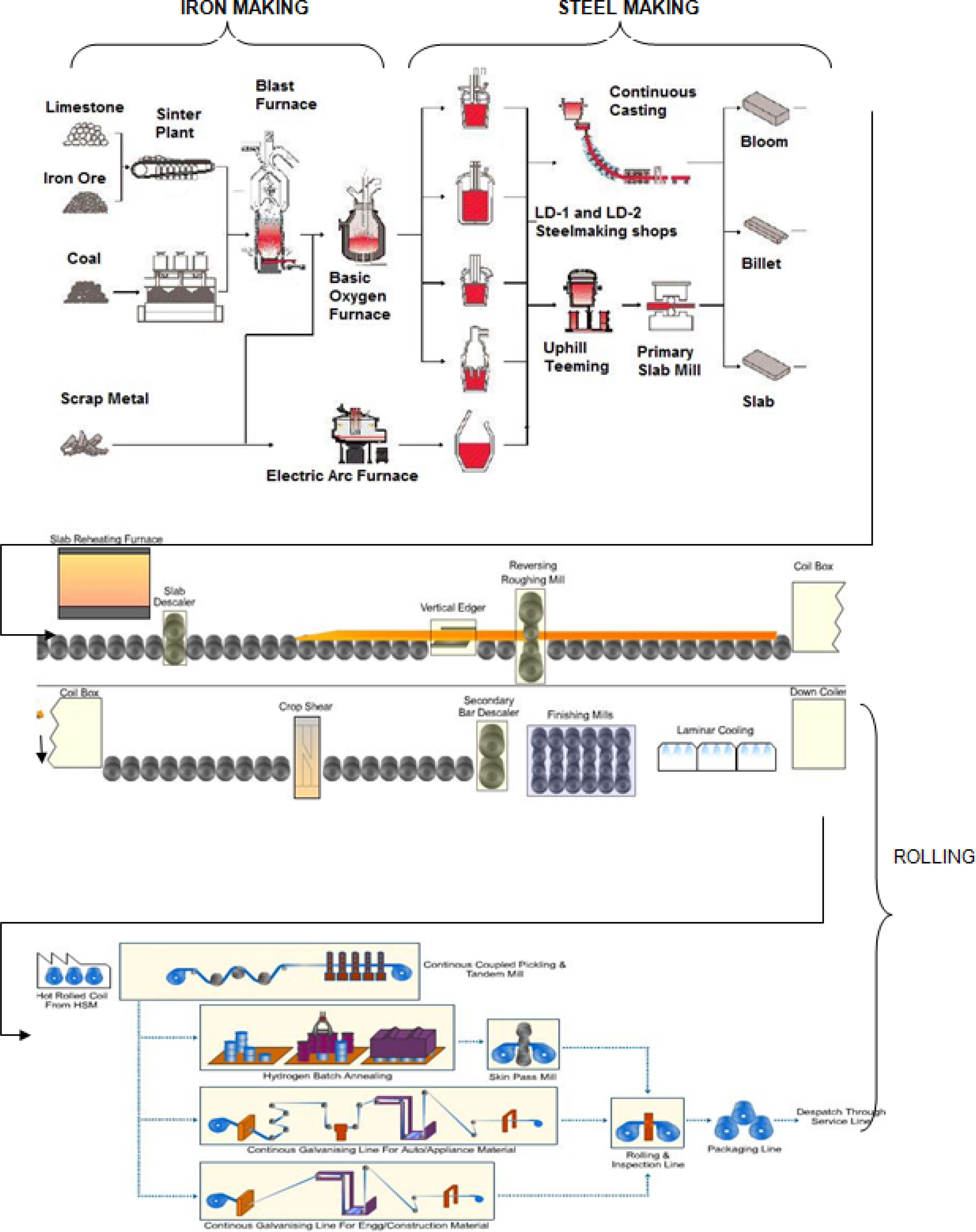
Figures Ref: “Making and rolling Steel” process – Tata Steel Europe document and http://tatasteelindia.com/products-and-processes/processes/steel-making-process.asp
Exhibit 8: Decision Tree – Sample
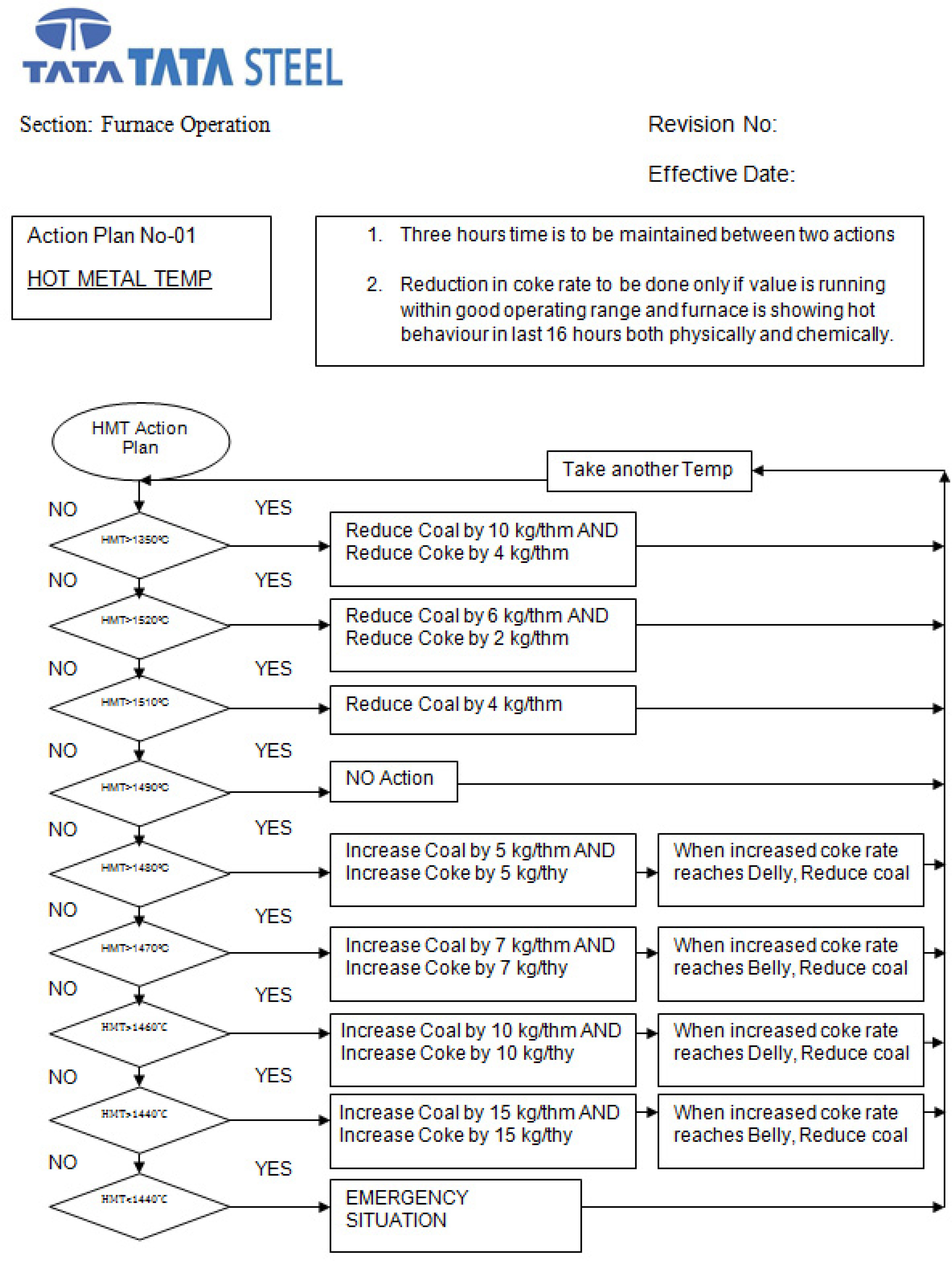
Ref: “Daily Management- The TQM Way”. By- Yukihiro Ando and Pankaj Kumar
Sign in to access this content
Get a 30 day free trial, more like this, sage recommends.
We found other relevant content for you on other Sage platforms.
Have you created a personal profile? Login or create a profile so that you can save clips, playlists and searches
- Sign in/register
Navigating away from this page will delete your results
Please save your results to "My Self-Assessments" in your profile before navigating away from this page.
Sign in to my profile
Please sign into your institution before accessing your profile
Sign up for a free trial and experience all Sage Learning Resources have to offer.
You must have a valid academic email address to sign up.
Get off-campus access
- View or download all content my institution has access to.
Sign up for a free trial and experience all Sage Learning Resources has to offer.
- view my profile
- view my lists
- +91- 9640901313 [email protected]
- Search for a Case
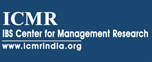
- Case Studies
Tata Steel`s Journey of Implementing TQM

Introduction
In March 2020, one of the top global steel companies, India-based Tata Steel Ltd. (Tata Steel), found a place for itself on the 2020 honors list of the US-based American Productivity and Quality Center (APQC) for ‘Excellence in Knowledge Management’..
Buy this case study (Please select any one of the payment options)
Copyright © 2020 - 2025 All Rights Reserved - icmrindia.org
