Academia.edu no longer supports Internet Explorer.
To browse Academia.edu and the wider internet faster and more securely, please take a few seconds to upgrade your browser .
Enter the email address you signed up with and we'll email you a reset link.
- We're Hiring!
- Help Center
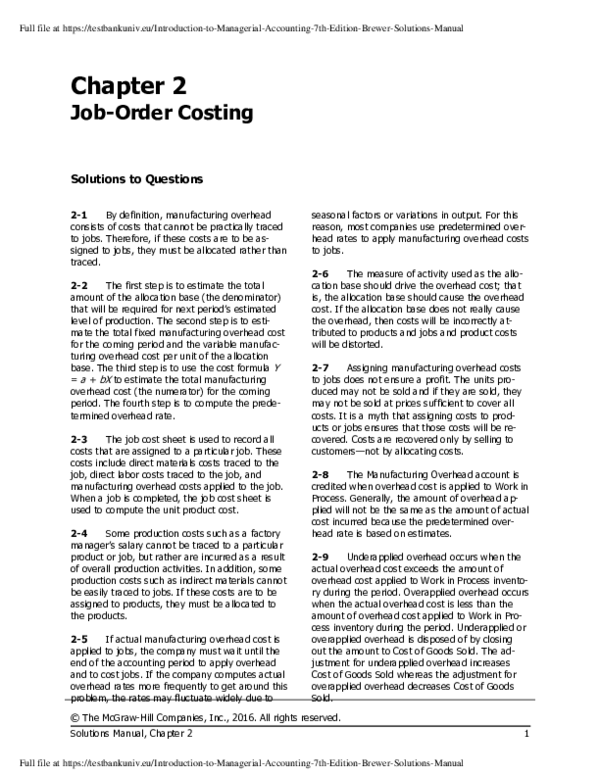

Chapter 2 Job-Order Costing

Related Papers
Bulend Terzioglu
In the early 1920s, direct labour comprised most of the total cost of manufacturing, and allocating overheads using direct labour hours or direct labour cost was sufficient for inventory valuation purposes, which was then the primary object of cost accounting. However, the upsurge of manufacturing overhead as a percentage of manufacturing cost at the expense of direct labour and proliferation of product lines complicated the otherwise relatively straightforward process of overhead cost allocation. Empirical evidence demonstrates that our understanding of how best to allocate overheads is at a nascent stage, and surprisingly most managers still do not know their costs. Moreover, managers have grave concerns about the current practice that allocates overheads to products in an arbitrary fashion. These concerns stem from the fact that managerial decisions are based on cost information furnished by management accountants, which is ostensibly inaccurate. This conceptual discussion paper ...
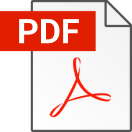
Cédric Lesage
Research Journal of Finance and Accounting
JOSEPH DWOMMOR
Glenn Ballard
ABSTRACT Construction projects become complicated and fragmented so that many specialty contractors are involved. In such changed environments, a general contractor's overhead costs are increasing comparable to direct costs. In addition to an increase of volume, activities consisting of overhead costs play an important role in coordinating different participants who include different specialty contractors and client.
ENTRENOVA - ENTerprise REsearch InNOVAtion
Székely Csaba
The development of overhead costs management is becoming more and more important as the percentage of overhead costs is rising. The last 15 years have demonstrated the awakening of advanced methods and tools aimed at understanding the utilization of overheads better. The paper investigates the current state of overhead costs management using a sample of 20 companies in Austria, Hungary, and Slovakia. A qualitative approach was applied in a multi-case study, which unveiled the significance of overhead cost management with the increasing trend of importance. The effort reflects current innovations using digitalization of processes. The findings show that (1) the majority of the companies indicated that digitalization heavily impacts overhead costs; (2) all expressed their dissatisfaction with the tools currently used; and (3) the majority cited that usability and speed are the predominant factors. The analysis and the subsequent synthesis delivered three theses: (1) perception that di...
Operations Management Research
Roger Schmenner
Journal of International Studies
Ján Dvorský
rupesh tembhare
Management Accounting Research
Alfred Wagenhofer
Journal of Accounting and Economics
Naomi Soderstrom
RELATED PAPERS
Norber Caramut
Luana Soares
Edmilson José Ambrosano
Iranian Journal of Ageing
abbas ramezani farani
Astrid Oberson
Tetrahedron Letters
Virgil Helaine
fabienne montmasson-michel
ANIL KUMAR MATTA
The 7th Iberian Congress on Cyanotoxins/3rd Iberoamerican Congress on Cyanotoxins
El Mahdi Redouane
Sharon Baute
INTERNATIONAL JOURNAL OF ENDORSING HEALTH SCIENCE RESEARCH (IJEHSR)
NADIA ISHAQ
Pediatric Infectious Disease Journal
CECILIA MARQUEZ
Statsvetenskaplig tidskrift
Elsa Hedling
Florence Weber
Cellular Immunology
Marie Lipoldova
Biophysical Chemistry
Fernando Dias
Optometry - Journal of the American Optometric Association
Remo Susanna
Diabetes Care
Kelly Mackintosh
Early Child Development and Care
Brenda Louw
IntechOpen eBooks
Ilias Gkotsis
Canadian Journal of Physiology and Pharmacology
Gordon Kirby
Gatis Muiznieks
See More Documents Like This
- We're Hiring!
- Help Center
- Find new research papers in:
- Health Sciences
- Earth Sciences
- Cognitive Science
- Mathematics
- Computer Science
- Academia ©2024
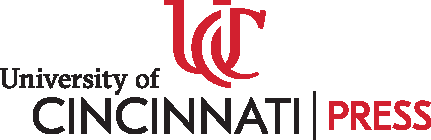
Want to create or adapt books like this? Learn more about how Pressbooks supports open publishing practices.
2 Job-order Costing
Learning Objectives LO
LO1 Describe a job-order costing system
LO2 Describe the flow of inventory costs in a job-order costing system
LO3 Calculate the organization-wide predetermined manufacturing overhead rate
LO4 Apply manufacturing overhead to jobs using an organization-wide predetermined manufacturing overhead rate
LO5 Complete a job-cost sheet and compute the total cost of a job, cost per unit, and selling price
LO6 Calculate multiple predetermined manufacturing overhead rates
Job-order costing LO1
Job-order costing is an accounting system used to assign manufacturing costs to the products or services that an organization produces. Product costs , or inventory costs, include the costs for direct material , direct labor , and manufacturing overhead . In a job-order costing system, product costs are assigned directly to the products or jobs as they are produced or completed.
Organizations that produce unique or custom products or services typically use a job-order costing system. For example, a construction company specializing in new home construction uses a job-order costing system. The costs for direct material, direct labor, and manufacturing overhead is assigned directly to the homes using the materials or labor. When a home is finished, the company has a record of the actual costs incurred to build each house.
The costs incurred during the manufacturing process are accumulated in inventory accounts within the organization’s accounting system. Inventory accounts are classified as assets. Assets are items that an organization owns that have future value to the organization. The inventory accounts commonly used in a job-order costing system include the Raw Materials account , Manufacturing Overhead account , Work in Process account , and Finished Goods account . Product costs, or manufacturing costs, flow through these accounts until the product is complete. The total cost to manufacture the finished product is held in the Finish Goods inventory account until the product is sold.
Once a product is sold, it is no longer an asset in the organization’s possession. At that point, the costs to manufacture the product are moved from the Finished Goods inventory asset account to the Cost of Goods Sold account. Cost of goods sold is classified as an expense account. At the same time, the revenue collected from the sale is recorded in the Sales revenue account. The sales revenue less the cost of goods sold equals the gross profit made on the product. Period costs are deducted from gross profit to arrive at net operating income, also referred to as net profit.
Check your understanding LO1
Job-order costing flow of inventory costs LO2
The inventory asset accounts and expense accounts used in a job-order costing system are discussed in detail in this section. The accounting terms of debit and credit are used to identify the increases and decreases made to each account during the process. A summary of the accounting equation and the accounting rules of debit and credit are provided in Exhibit 2-1 below. Additionally, the flow of costs in a job-order costing system is demonstrated in Video Illustration 2-1.
Exhibit 2-1 Accounting equation and rules for debits and credits

Raw materials (direct and indirect)
The costs for all raw materials—direct and indirect—purchased to manufacture the product are debited to the Raw Materials account . The credit for raw materials costs is typically recorded in the Cash account or a related liability account. Direct materials are raw materials that can be easily and economically traced to the production of the product. Indirect materials are raw materials that cannot be easily and economically traced to the production of the product, e.g. glue, nails, sandpaper, towels, etc.
When materials are requisitioned for manufacturing, all materials are credited out of the Raw Materials inventory account. Direct materials are debited into the Work In Process inventory account and indirect materials are debited to the Manufacturing Overhead account .
The costs for direct labor is debited to the Work In Process inventory account and indirect labor is debited to the Manufacturing Overhead account . Typically, a liability account such as Salaries Payable is credited. Direct labor costs are manufacturing labor costs that can be easily and economically traced to the production of the product. Indirect labor costs are manufacturing labor costs that cannot be easily and economically traced to the production of the product, e.g. the production supervisor’s salary or quality control.
Non-manufacturing labor costs, such as office or administrative wages, are period costs . Non-manufacturing labor costs are debited to an expense account for wages or salaries. A liability account such as Salaries Payable is credited.
Manufacturing overhead
Actual manufacturing overhead costs are debited to the Manufacturing Overhead account as they are incurred. The credit for these costs is typically recorded in the Cash account or a related liability account. Manufacturing overhead costs include all indirect costs associated with manufacturing the product that are not direct material or direct labor , such as indirect materials , indirect labor , and all other production costs incurred to run the production facility, e.g. rent, utilities, janitorial services, and taxes on the production facility. For example, when the rent or property taxes are paid on the production factory the Manufacturing Overhead account is debited and the Cash account is credited.
Manufacturing overhead costs are applied to the jobs in process using a predetermined manufacturing overhead rate . The predetermined manufacturing overhead rate is discussed in detail in subsequent sections of this chapter. When manufacturing overhead is applied to the jobs in process, it is credited from the Manufacturing Overhead account and debited to the Work In Process account.
Work in process (WIP)
Work in Process (WIP) is the inventory account where product costs–direct material, direct labor, and manufacturing overhead–are accumulated while the jobs are in the manufacturing process.
Finished goods
When a job is finished, the total costs for the job are moved from the Work In Process inventory account (credit) to the Finished Goods inventory account (debit). The Finished Goods inventory account is where finished inventory is reported at the cost to produce—direct material, direct labor, and manufacturing overhead—until it is sold.
Cost of goods sold
When the inventory is sold, the total costs for the job are moved from the Finished Goods inventory account (credit) to the Cost of Goods Sold expense account (debit). Cost of Goods Sold is the expense account used to report the costs associated with purchasing or manufacturing the inventory sold.
Sales revenue is also recorded when the job is sold. Gross profit for the job is calculated as the sales revenue collected from the customer less the cost of the goods sold. In a job-order costing system, cost of goods sold represents total production costs, e.g. direct material , direct labor , and manufacturing overhead .
Video Illustration 2-1: Demonstrating cost flow in a job-order costing system LO2
A chart of accounts is presented in Exhibit 2-1 to demonstrate the cost flow in a job-order costing system. The chart is arranged using the accounting equation format, Assets = Liabilities + Equity. The chart includes T-accounts for the accounts commonly used in a job-order costing system. The job-order costing flow is described in detail in Video Illustration 2-1.
Exhibit 2-2 Chart of accounts used for job-order cost accounting and video explanation
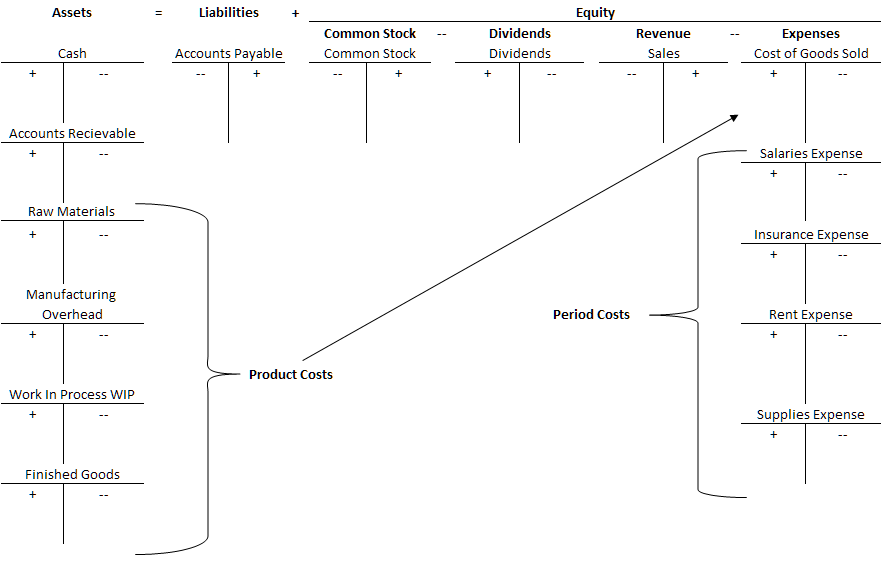
Check your understanding LO2
Predetermined manufacturing overhead rate LO3
All manufacturing, or product costs , that are not direct material or direct labor , are recorded in the Manufacturing Overhead account . Direct material and direct labor are applied directly to the jobs and do not flow through the Manufacturing Overhead account. Manufacturing overhead includes indirect materials, such as glue, screws, and nails; indirect labor, such as wages for the production supervisor or production maintenance personnel; and all other costs incurred to manufacture a product, such as rent, insurance, taxes, and utilities paid for the manufacturing facilities.
Manufacturing overhead is applied to jobs using a predetermined manufacturing overhead rate . Unlike direct material or direct labor , it not easy to apply manufacturing overhead costs directly to jobs. Manufacturing overhead costs are not incurred uniformly and many of these costs are not directly traceable to the jobs in process. For example, an organization might pay property taxes on the production plant twice a year. These property taxes are considered indirect manufacturing costs and should be applied to all jobs produced during the year and not just the jobs in process at the time the taxes are paid.
Think of manufacturing overhead as a pool or bucket of all indirect product costs. At the beginning of the period, the total amount of manufacturing overhead costs are estimated based on historical data and current year production estimates. Throughout the year, the total amount of estimated manufacturing overhead is uniformly applied to the jobs in process using some type of allocation base or cost driver. An allocation base or cost driver is a production activity that drives costs. Common allocation bases are direct labor hours, machine hours, direct labor dollars, or direct materials dollars. At the end of the year, the estimated applied overhead costs and actual overhead costs incurred are reconciled and any difference is adjusted.
An organization-wide, or organizational, predetermined manufacturing overhead rate is computed by dividing the total estimated manufacturing overhead amount by the total estimated allocation base or cost driver. Total estimated overhead includes all product costs and is commonly separated into fixed manufacturing overhead and variable manufacturing overhead. Allocation bases will vary across organizations. For example, an organization that produces a labor intensive product might select direct labor hours as the allocation base. Whereas, an organization that relies on machines instead of laborers might use machine hours as the allocation base.
The formula for computing an organization-wide predetermined manufacturing overhead rate is presented in Exhibit 2-3.
Exhibit 2-3 Formula for organization-wide predetermined manufacturing overhead rate.

Video Illustration 2-2 : Computing an organization-wide predetermined manufacturing overhead rate LO3
The processes to solve the following scenario are demonstrated in Video Illustration 2-2 below. Cincy Chips produces microchips for small electronic devices. On January 1, Cincy Chips estimates that they will produce 50,500 microchips and run 2,080 machine hours in the upcoming year. The company uses a organization-wide manufacturing overhead rate . Manufacturing overhead is allocated to jobs based on machine hours. The cost formula to estimate manufacturing overhead at the beginning of the year is $128,960 fixed plus $33 variable overhead per machine hour. Compute the organization-wide predetermined manufacturing overhead rate using the template provided in Exhibit 2-4.
Exhibit 2-4 Formula for organizational predetermined manufacturing overhead rate and video explanation

Check your understanding LO3
Applying manufacturing overhead to jobs LO4
The predetermined manufacturing overhead rate is computed before the period starts, usually at the beginning of a year or quarter. Manufacturing overhead is then applied to the jobs as the work is completed throughout the year. In a job-order costing system, the predetermined overhead rate is applied to the jobs based on the job’s actual use of the allocation base or cost driver used to calculate the predetermined rate.
Video Illustration 2-3: Applying manufacturing overhead to jobs LO4
The processes to solve the following scenario are demonstrated in Video Illustration 2-3 below. Cincy Chips produces microchips for small electronic devices. The predetermined manufacturing overhead rate is $95 per machine hour (total estimated overhead $197,600 / 2,080 total estimated machine hours). Job 36A was for 75 microchips and used 3.5 machine hours. Compute the manufacturing overhead applied to Job 36A.
Exhibit 2-5 Applying overhead to jobs video explanation

Check your understanding LO4

Job cost sheets LO5
All manufacturing costs incurred to complete a job are recorded on job cost sheets. Job cost sheets can be kept on physical paper or digitally. A standard job cost sheet records all direct material , direct labor , and manufacturing overhead costs applied to a job. Typically, a job cost sheet also records the total costs, the number of units, the cost per unit, as well as the selling price for each job.
Video Illustration 2-4 : Completing a job cost sheet LO5, LO7
The processes to solve the following scenario are demonstrated in Video Illustration 2-4 below. Cincy Chips produces microchips for small electronic devices. The predetermined manufacturing overhead rate is $95 per machine hour. Job 69B was for 500 microchips and used 22 machine hours. Production used $13,500 of direct material and worked 21 direct labor hours at a rate of $20 per hour. Complete the job cost sheet for Job 69B given in Exhibit 2-6.
Exhibit 2-6 Job cost sheet and video explanation
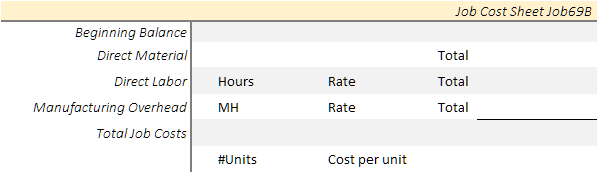
Check your understanding LO5, LO7
Multiple predetermined manufacturing overhead rates LO6
In some cases, organizations choose not to use a single, organization-wide predetermined manufacturing overhead rate to apply manufacturing overhead to the products or services produced. In the preceding sections, an organization-wide predetermined manufacturing overhead rate was calculated. Many organizations have multiple departments or processes that consume different amounts of manufacturing overhead resources at different rates. In these organizations, a single manufacturing overhead rate, while more simplistic, may not accurately apply overhead to the final product. An organization with multiple departments or processes may choose to apply manufacturing overhead using multiple predetermined manufacturing overhead rates. When multiple predetermined manufacturing overhead rates are used, manufacturing overhead costs are allocated to specific departments or processes and then applied to jobs using an allocation base that drives the overhead costs for that department or process.
Before multiple predetermined manufacturing overhead rates can be computed, manufacturing overhead costs must be assigned to departments or processes. Then the departmental or process manufacturing overhead rate is computed by dividing the total estimated manufacturing overhead assigned to the department or process by the total estimated allocation base or cost driver incurred within that department or process.
It is important to note, that only manufacturing overhead costs that are allocated to the department or process as well as the allocation base or cost driver incurred within the same department or process are used to compute a departmental predetermined manufacturing overhead rate.
The formula for computing the departmental predetermined manufacturing overhead rates is presented in Exhibit 2-7.
Exhibit 2-7 Formula for departmental predetermined manufacturing overhead rates.

Video Illustration 2-5 : Computing multiple predetermined manufacturing overhead rates LO6
The processes to solve the following scenario are demonstrated in Video Illustration 2-5 below. SunCo, Inc. manufactures widgets. The manufacturing process has two departments—fabrication and finishing. In the fabrication department, laborers pour composite materials into custom carved molds. Fabrication is a labor intensive process. After molding, the widgets are sent to the finishing department. In finishing, the widgets are put on an automated production line where they are heated and coated. Finishing is a machine intensive process.
SunCo, Inc. assigns manufacturing overhead to the products produced using departmental predetermined manufacturing overhead rates. Manufacturing overhead is applied based on labor hours in the fabrication department and machine hours in the finishing department. Relevant data are provided in Exhibit 2-8. Compute the departmental predetermined manufacturing overhead rates for the fabrication and finishing departments.
Exhibit 2-8 Data for departmental predetermined manufacturing overhead rates and video explanation.
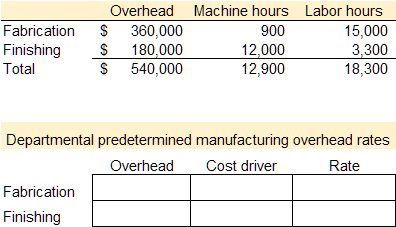
Check your understanding LO6
Practice Video Problems
The chapter concepts are applied to comprehensive business scenarios in the below Practice Video Problems.
Practice Video Problem 2-1: Compute organizational predetermined manufacturing overhead rate, total job costs, and selling price LOs3,4,5,7
Kelly Shuck Productions uses a job-order costing system. At the beginning of the year, the company made the following estimates:
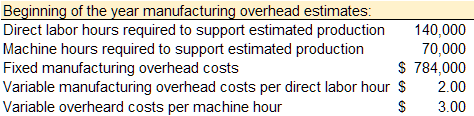
During the year, Job KAS3 was started and completed. The following information is available with respect to this job:
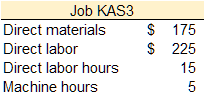
Required 1: Compute the organization-wide predetermined manufacturing overhead rate (single rate for the entire organization) with direct labor hours as the allocation base.
Required 2: Assume that Kelly uses the organizational predetermined manufacturing overhead rate calculated in requirement 1. Compute the total manufacturing cost of Job KAS3.
Required 3: If Kelly uses a markup percentage of 200% of its total manufacturing cost, what is the selling price for Job KAS3 (based on the total costs of computed in requirement 2)?

Practice Video Problem 2-2: Compute organizational predetermined manufacturing overhead rate, total job costs, and selling price LOs3,4,5,7
Required 1 : Compute the organizational predetermined manufacturing overhead rate (single rate for the entire organization) with machine hours as the allocation base.
Required 2 : Assume that Kelly uses the organizational predetermined manufacturing overhead rate calculated in requirement 1. Compute the total manufacturing cost of Job KAS3.
Practice Video Problem 2-3: Compute departmental predetermined manufacturing overhead rates, total job costs, and cost per unit LOs 4,5,6,7
Rookwood Pottery makes a variety of pottery products that it sells to retailers. The company uses a job-order costing system. Relevant data are provided below.
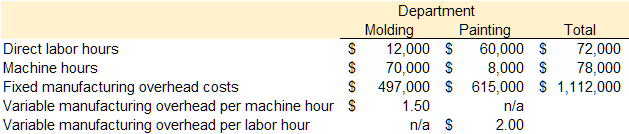
The following information was recorded for Job B53, which was started and completed during the year.
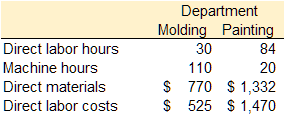
Required 1: Assume that Rookwood uses departmental predetermined manufacturing overhead rates to apply manufacturing overhead costs to jobs. The predetermined manufacturing overhead rate in the Molding Department is based on machine-hours, and the rate in the Painting Department is based on direct labor-hours. Compute the predetermined manufacturing overhead rates used in the Molding Department and the Painting Department.
Required 2: Assume that Rookwood uses the departmental predetermined manufacturing overhead rates calculated in requirement 1. Compute the total costs of Job B53.
Required 3: If Job B53 contained 50 units, compute the cost per unit (based on the total costs of Job B53 computed in requirement 2).
Review Questions
Review questions reinforce the chapter content.
Homework Questions
Homework questions can be used for additional practice or can be assigned in an academic setting. Full feedback is not available online. Homework questions can be assigned, with auto-grading and export, to specific learning management platforms, e.g., Canvas, Blackboard, etc. Contact the author for details.
Homework 2-1
Homework 2-2
Homework 2-3
Homework 2-4
Homework 2-5
Homework 2-6
Job-order costing is an accounting system used to assign costs to the products or services that an organization produces.
Product costs are all costs associated with purchasing or producing inventory for resale.
Direct materials are raw materials costs that can be easily and economically traced to the production of the product.
Direct labor is manufacturing labor costs that can be easily and economically traced to the production of the product.
Manufacturing overhead are all other indirect costs associated with manufacturing the product that are not direct material or direct labor.
Assets are items that an organization owns that have future value to the organization.
The Raw Materials inventory account is used to record the costs for all raw materials—direct and indirect—purchased to manufacture a product.
The Manufacturing Overhead inventory account is used to record actual manufacturing overhead costs incurred to produce a product.
Work in Process (WIP) is the inventory account where product costs including direct material, direct labor, and manufacturing overhead are accumulated while the jobs are in the manufacturing process.
The Finished Goods inventory account is where finished inventory is reported at the cost to produce—direct material, direct labor, and manufacturing overhead—until it is sold.
An expense is a cost of operations that a company incurs to generate revenue. Generally, the benefit of the cost is used in the same period in which the corresponding revenue is reported.
Sales revenue is the income received by a company from its sales of goods or the provision of services.
Cost of Goods Sold is the expense account used to report the costs associated with purchasing or manufacturing the inventory sold.
Gross profit is sales revenue less the cost of the goods sold.
Period costs are all other costs not associated with purchasing or producing inventory for resale but are necessary for sustaining the organization, selling the inventory, and servicing customers.
A liability is a present obligation for an organization to provide cash or some other service in the future. Examples of common liability accounts include, Accounts Payable, Salaries Payable, or Taxes Payable.
Indirect materials are raw materials that cannot be easily and economically traced to the production of the product, e.g. glue, nails, sandpaper, towels, etc.
Indirect labor costs are manufacturing labor costs that cannot be easily and economically traced to the production of the product, e.g. the production supervisor’s salary or quality control.
Estimated overhead rate used to uniformly apply estimated manufacturing overhead to the jobs in process during a specified period of time using some type of allocation base or cost driver, such as direct labor hours, direct material dollars, or machine hours.
An allocation base or cost driver is a production activity that drives costs such as direct labor hours, machine hours, direct labor dollars, or direct material dollars.
An organization-wide predetermined manufacturing overhead rate is computed by dividing the total estimated manufacturing overhead amount by the total estimated allocation base or cost driver.
A standard job cost sheet records all direct material, direct labor, and manufacturing overhead costs applied to a job.
When multiple predetermined manufacturing overhead rates are used, manufacturing overhead costs are allocated to specific departments or processes and then applied to jobs using an allocation base or cost driver that drives the overhead costs for that department or process.
Principles of Managerial Accounting Copyright © 2020 by Dr. Patricia Goedl is licensed under a Creative Commons Attribution 4.0 International License , except where otherwise noted.
Share This Book

Fetty Ade Putri Universitas Potensi Utama, Medan, North Sumatra, Indonesia Indonesia
Efani Desi Universitas Potensi Utama, Medan, North Sumatra, Indonesia Indonesia
Documents | Secondary documents
- Focus and Scope
- Editorial Team
- Open Access Policy
- Author Guidelines
- Publication Ethics
- Online Submission
- Peer Review Process
- Plagiarism Checking
- Copyright Transfer Agreement
- Retraction Policy
- Author(s) Fee
- Recommend to Librarian
- Recommend to Colleague
- Vol.6, No.6, April 202 3
- Vol.6, No.5, February 202 3
- Vol.6, No.4, December 202 2
- Vol.6, No.3, October 202 2
- Vol.6, No.2, August 202 2
- Vol.6, No.1, June 202 2
- Vol.5, No.6, April 202 2
- Vol.5, No.5, February 202 2
- Vol.5, No.4, December 2021
- Vol.5, No.3, October 2021
- Vol.5, No.2, August 202 1
- Vol.5, No.1, June 202 1
- Vol.4, No.2, May 202 1
- Vol.4, No.1, November 2020
- Vol.3, No.2, May 2020
- Vol.3, No.1, November 2019
- Vol.2, No.2, May 2019
- Vol.2, No.1, November 2018
- Vol.1, No.2, May 2018
- Vol.1, No.1, November 2017
EDITOR IN CHIEF

Associate Professor Tutut Herawan, PhD STIKOM Tunas Bangsa, Pematangsiantar North Sumatera, Indonesia Web of Science ResearcherID: AAB-6534-2021 Scopus ID: 35085139400

Cost of Production Price Analysis Using Job Order Costing Method In CV. Alam Lestari Jaya
Cost of production is the cost of production absorbed into each unit of product produced by the company. Calculation of order costs is a method for determining the cost of production of a company's products according to consumer orders. CV. Alam Lestari Jaya is a company engaged in the field of convection and processing of clothing materials into ready-made clothes for various purposes. The purpose of this research is to find out how to CV. Alam Lestari Jaya determines the cost of production and compares it with the job order costing method. This research uses experimental methods, quantitative descriptive data analysis, and observation. The result is that CV Alam Lestari Jaya can apply the job order costing method to calculate the cost of production. As a result, the difference in cost of goods manufactured, which shows lower costs than using the job order costing method. There is a difference in the selling price of Rp 2.817, according to the company and the calculated job order costing. Besides, this study did not calculate all factory overhead costs because the company did not allocate a budget for factory overhead costs. This causes factory overhead costs not to be fully calculated, such as electrical loads and depreciation loads for sewing machines. The final results obtained in this study are in accordance with the expected criteria.
Sujarweni, V. Wiratna. "Cost Accounting Theory and Its Application." (2015).
Rumampuk, Maria Sifra. "Comparison of Product Cost Calculation Using the Activity Based Costing Method and Conventional Method in Cv. Kharis Chicken Farming Business in Bitung City." EMBA Journal: Journal of Economic, Management, Business and Accounting Research 1.4 (2013).
Bustami, Bastian. "Nurlela. 2006." Cost accounting.
Otto Fajarianto, Muchammad Iqbal and Jaka Tubagus Cahya, 2017, Support System Employee Acceptance Selection Decision Using Weighted Product Method, Vol. 7 No. 1.
Si, Irwanto-M., Putra Randa, and Juliani Juliani. "Analysis Of Job Order Costing In Independent Media." Bus-A Journal: Journal of Business Administration 6.2 (2017): 37-46.
Lasena, Sitty Rahmi. "Analysis of Determination of Cost of Production at PT. Dimembe Nyiur Agripro." EMBA Journal: Journal of Economic, Management, Business and Accounting Research 1.3 (2013).
Coal, Helmina. "The determination of the cost of production is based on the full costing method in the manufacture of glass and aluminum display cases in UD. Palace of Aluminum Palace." EMBA Journal: Journal of Economic, Management, Business and Accounting Research 1.3 (2013).
Setiadi, Pradana. "Calculation of Cost of Production in Determining Selling Prices on the CV. Minahasa Masa Perkasa. "Periodical Journal of Scientific Efficiency 14.2 (2014).
Mukhtar, M., and M. Guardian. "Cost of Production System with Job Order Costing Approach and Its Effect on Operating Profit." Journal of Management and Business Economics (EMBis) 2.2 (2014): 345-355.
Kusumawardani, Rully. "Calculation of Cost of Production Using the Job Order Costing Method (Case Study of UMKM CV. TRISTAR Aluminum)." Journal of the Faculty of Economics and Business, University of Brawijaya Malang (2013).
Handayani, Yunita. Evaluation of Determination of Cost of Production with the Job Order Method Costing on Pradan Furniture Surakarta. Diss Eleven University in March, 2005
- There are currently no refbacks.
Jumlah Kunjungan:
View My Stats

IJISTECH (International Journal of Information System and Technology) ISSN | 2580-7250 (online) Organized by LPPM STIKOM Tunas Bangsa Published by STIKOM Tunas Bangsa W: http://ijistech.org/ijistech/index.php/ijistech

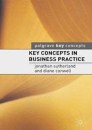
Key Concepts in Business Practice pp 142–151 Cite as
- Jonathan Sutherland &
- Diane Canwell
45 Accesses
Part of the book series: Palgrave Key Concepts ((KCS))
This is a preview of subscription content, log in via an institution .
Unable to display preview. Download preview PDF.
Wall, Toby and Parker, Sharon, Job and Work Design: Organizing Work to Promote Well-Being and Effectiveness . London: Sage Publications, 1998.
Google Scholar
Peters, Tom, Projects 50: Or, 50 Ways to Transform Every ‘Task’ into a Project that Matters . New York: Alfred A. Knopf, 1999.
Savall, Henri, Work and People: An Economic Evaluation of Job-enrichment . Oxford: Oxford University Press, 1981.
Quaid, Maeve, Job Evaluation: The Myth of Equitable Assessment . Toronto: University of Toronto Press, 1996.
Robbins, Stephen and Coulter, Mary, Management . New York: Prentice-Hall, 2001.
Robbins, Stephen, Organizational Behaviour . Englewood Cliffs, NJ: Prentice-Hall, 2003.
Brannick, Michael T. and Levine, Edward L., Job Analysis: Methods, Research and Applications for Human Resource Management in the New Millennium . Thousand Oaks, CA: Sage Publications.
Delbridge, Rick, Life on the Line in Contemporary Manufacturing: The Workplace Experience of Lean Production and the ‘Japanese’ Model . Oxford: Oxford University Press, 2000.
McInnis, Kenneth R., Kanban Made Simple: Demystifying and Applying Toyota’s Legendary Manufacturing Process . New York: Amacom, 2003.
Download references
You can also search for this author in PubMed Google Scholar
Copyright information
© 2004 Jonathan Sutherland and Diane Canwell
About this chapter
Cite this chapter.
Sutherland, J., Canwell, D. (2004). Jj. In: Key Concepts in Business Practice. Palgrave Key Concepts. Palgrave, London. https://doi.org/10.1007/978-0-230-21179-7_10
Download citation
DOI : https://doi.org/10.1007/978-0-230-21179-7_10
Publisher Name : Palgrave, London
Print ISBN : 978-1-4039-1531-3
Online ISBN : 978-0-230-21179-7
eBook Packages : Palgrave Business & Management Collection Business and Management (R0)
Share this chapter
Anyone you share the following link with will be able to read this content:
Sorry, a shareable link is not currently available for this article.
Provided by the Springer Nature SharedIt content-sharing initiative
- Publish with us
Policies and ethics
- Find a journal
- Track your research

IMAGES
VIDEO
COMMENTS
Abstract. In this paper, two new optimization models for Activity Based Costing (ABC) and Traditional costing techniques in the manufacturing field within a job shop manufacturing environment will be considered. The two models take into consideration the bi- directional relationship between hourly rates and annual hours on each machine.
This paper addresses job costing, activity-based costing, cost management and cost control in Kenya and Unilever Kenya. The paper provides a glimpse of how these cost structured are practised.
This paper is a review and comparison of two common costing methods. In order to succeed in business, it is prudent to understand the flow of cash and resulting financial information. This ...
Find a journal Publish with us Track your research Search. Cart. Handbook Integral Logistics Management pp 681-714Cite as. Home. Handbook Integral Logistics Management. Chapter. Cost Estimation, Job-Order Costing, and Activity-Based Costing Cost Estimation, Job-Order Costing, and Activity-Based Costing ...
This research uses experimental methods, quantitative descriptive data analysis, and observation. The result is that CV Alam Lestari Jaya can apply the job order costing method to calculate the cost of production. As a result, the difference in cost of goods manufactured, which shows lower costs than using the job order costing method.
Using job cost data from a leading printing company in Taiwan, this study empirically examines product pricing behavior both before and after a change in the job order costing system. As direct ...
Research and development Production Procurement Data management: representation and systems management of logistic objects ... Thirdly, job-order costing must be carried out as soon as possible after the order is completed. Invoices, the source of information on actual costs for external operations and . 684 16 Cost Estimation, Job-Order ...
Job and Batch Costing 73 In this chapter we look first at the procedures involved and how job costs are collected. We then go on to examine how the cost of a job or batch is calculated. 8.2 Job Costing Procedures Job costing is used when customers specify their requirements and the job relatively small and short in duration.
The purpose of this case study is to understand and evaluate the costing method currently employed by a company in the Dayton, OH area1, and identify the most beneficial costing method for its circumstances. Background research on common costing methods including traditional, process, job, activity-based, and variable is used to analyze the ...
Academia.edu is a platform for academics to share research papers. Product Costing and Cost Accumulation in a Batch Production Environment ... 3-3 Types of Product-Costing Systems Process Job-Order Costing Costing Used for production of large, unique, high-cost items. Built to order rather than mass produced. ...
firm, job costing means the linking of work, activity, time, place, and money) to a specific item or batch of items. In relation to cost accounting, Kohler (1970) defines job costing as 'a method of 1 The terms 'specific order', 'production order', 'job lot cost system' and 'job order costing' are also used. 57 W. A. Layne, Cost Accounting
When the actual machine-hours turn out to be 75,000, the costing system assumes that the overhead will be 75,000 machine-hours × $2.40 per machine-hour, or $180,000. This is a drop of $12,000 from the initial estimated manufacturing overhead cost of $192,000.
Job-order costing LO1. Job-order costing is an accounting system used to assign manufacturing costs to the products or services that an organization produces. Product costs, or inventory costs, include the costs for direct material, direct labor, and manufacturing overhead.In a job-order costing system, product costs are assigned directly to the products or jobs as they are produced or completed.
Discover the world's research. 25+ million members; 160+ million publication pages; 2.3+ billion citations; ... but in normal historical job order costing, actual time consumed is the measure of .
Method used in this research is direct and indirect interview, and literature study. Furthermore, the evaluation was done on the research conducted by comparing ... ie process costing and job order costing, and View metadata, citation and similar papers at core.ac.uk brought to you by CORE provided by Jurnal Online Universitas 45 Surabaya. 7
Step 5: Compute the rate per unit. • Actual indirect cost rate is $65,100 ÷ 2,480 = $26.25 per machine hour. General Approach to Job Costing. Step 1: The cost object is Job 100. Step 2: Identify the direct costs of Job 100. Step 3: Select the cost-allocation base. Step 4: Identify the indirect costs.
This research uses experimental methods, quantitative descriptive data analysis, and observation. The result is that CV Alam Lestari Jaya can apply the job order costing method to calculate the cost of production. As a result, the difference in cost of goods manufactured, which shows lower costs than using the job order costing method.
Job costing The term 'job costing' refers to the process of identifying a specific cost unit and then identifying the costs attributed to that cost unit. This process is imperative as it is the basis upon which a business sets its selling price, whilst ensuring that costs incurred on that job are kept within a fixed price band.
Download Citation | On Sep 3, 2018, Paul Schönsleben published Cost Estimating, Job-Order Costing, and Activity-Based Costing | Find, read and cite all the research you need on ResearchGate
As an example, if the factory overhead budget for the upcoming year is $150,000 and the direct labor budget is $100,000 the predetermined factory overhead rate would be 150% of direct labor ($150,000 / $100,000 = 150%). The process of allocating factory overhead to jobs is called applying factory overhead.
In the use of job cost data from Erbil's leading bakery store, this research empirically examines item price conduct both before and after a shift in the costing scheme for work orders. Since direct material expenses are charged individually and labor costs are fixed, this business varies only by a minimal percentage of the labor costs. The main finding is that assigned fixed work expenses ...
Request PDF | On Jan 1, 2005, Zahirul Hoque published Job order costing | Find, read and cite all the research you need on ResearchGate
This paper evaluates the additional spending needed to meet core targets of selected Sustainable Development Goals (SDGs) while accounting for the associated cost to address climate risks. The SDGs under study are those related to human and physical capital development. An additional 3.8 percent of global GDP, or US$3.4 trillion, of public and private spending will be required by 2030 to ...
Job costing accounting or job order costing is a costing method in which costs are accumulated and analyzed by individual jobs or orders .. A job order costing system is used by entities that make ...